SINGLE/DOUBLE STAGE RADICAL SPLIT PUMP
A double scroll chamber structure is used in the pump body to lessen the radial force, lower shaft load, and increase the life of the bearings; centerline installation and end support structures can help the pump function better in high-temperature environments by raising its temperature. The height may lead to the pump body expanding and deforming; however, the pump body’s intake and outlet can be oriented in different ways to accommodate the user’s preferred pipeline configuration.
In order to lower the NPSH of the pump and lower the device’s installation cost, the single-stage configuration often uses a double-suction impeller. The first-stage double-suction and the second-stage impeller are typically used in two-stage structures, which allows the double-suction impeller to balance the axial force produced by itself at the same time. The pump’s cavitation requirements can be accommodated by both the first-stage double-suction and single-suction structures. The remaining axial force is supported by the bearing, and the secondary impeller uses a balance hole to balance the axial pressure. A two-stage single-suction face-to-face or back-to-back construction can be taken into consideration for operating situations that need low requirements on cavitation performance and high efficiency.
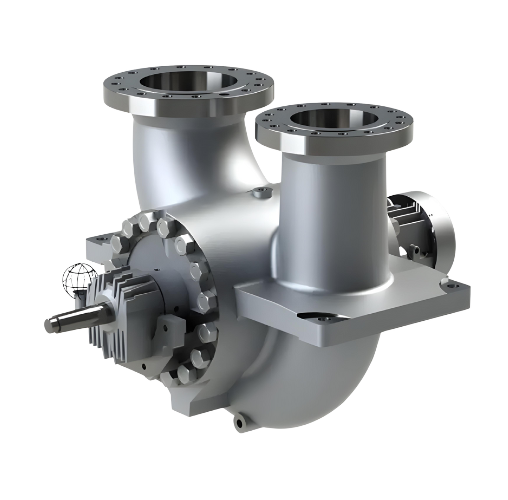
APPLICATIONS
- Clean or slightly polluted liquids
- General water supply
- Cooling water circulation
- Power plants’ district heating
- Pulp and paper.
- Pipelines
- Offshore platforms
OTHER TYPES OF CHEMICAL PUMP
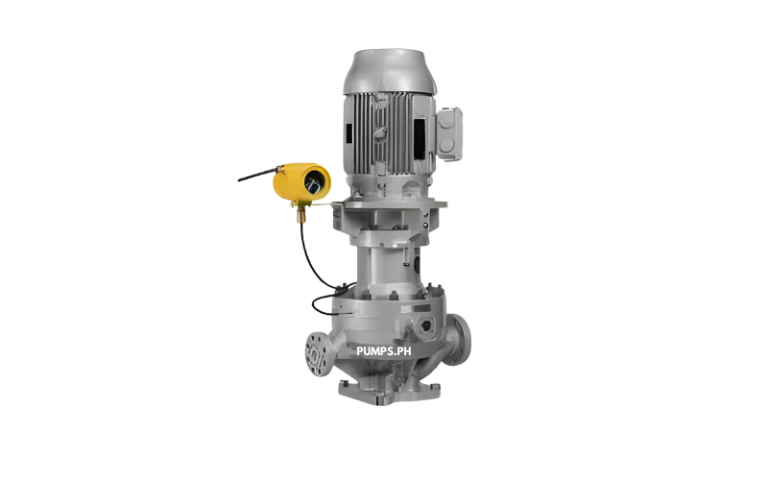
Vertical Inline Pump
The pump body and pump cover have a design pressure of 5.0 MPa, which creates a safe and dependable independent pressure chamber. There is a volute structure on the pump body. When the outlet measures 80 mm or more, the double volute structure effectively counteracts the radial force and maintains the rotor's stiffness. The pump cover has an extremely high degree of dependability, great pressure bearing capability, and rigid design.
- Clean or slightly polluted
- Low or high temperature
- Chemically neutral or corrosive liquids
- Refinery
- Oil and gas production.
- Petrochemical chemical industry
- Coal chemical industry
- Pipeline pressurization and offshore platforms and other fields with limited workspace.
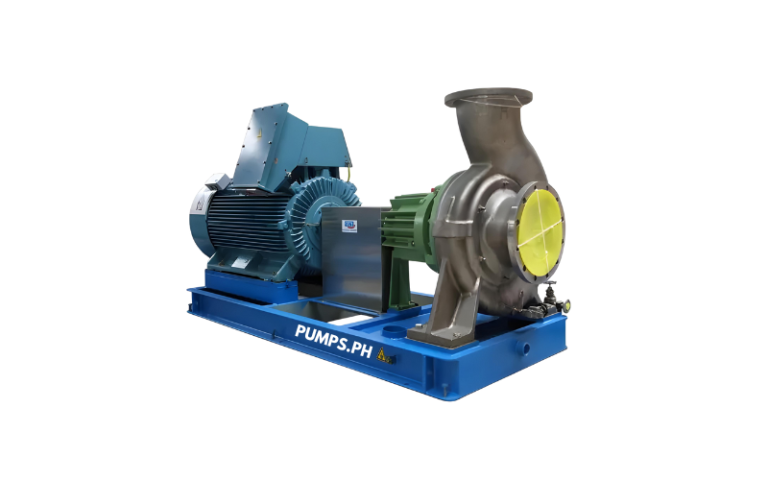
Petrochemical Process Pump
A horizontal, single-stage, radially split cantilever pump utilized in petrochemical processes is the OH1 series centrifugal pump. This kind of pump features a separate bearing box to support all forces applied to the pump shaft and keep the rotor position. The flexible coupling connects the driver of the pump to its base at the location of the pump.
- Clean or polluted, low or high temperature
- Chemically neutral or corrosive liquids
- Petrochemical
- Chemical industry
- Coal chemical
- Refinery
- Pulp and paper.
- District heating
- Fuel gas desulfurization and general industrial applications.
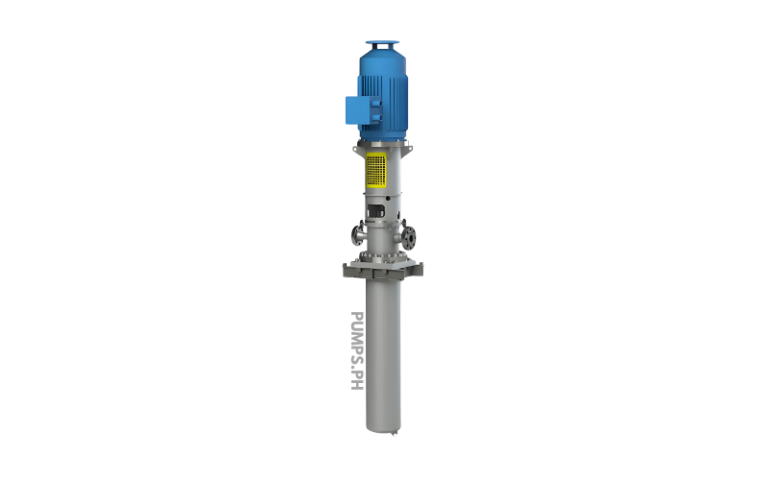
Vertical Barel Pump
It uses a multi-point support design, and the API 610 standard is satisfied by the support span between sliding bearings. In order to guarantee that the pump rotor has enough support stiffness, sliding bearings are also mounted at the suction port of the secondary impeller, before and after the first-stage impeller, and between the last-stage impeller and the inlet and outlet sections. Various working conditions can influence the choice of bushing material. For example, graphite impregnated with antimony, material composites, etc.
- Clean or slightly polluted low or high temperature chemically neutral or corrosive liquids
- Refinery
- Petrochemical industry
- Chemical industry
- Coal chemical industry
- Power station
- Cryogenic engineering
- Pipeline pressurized offshore platform.
- Liquefied gas engineering, etc.
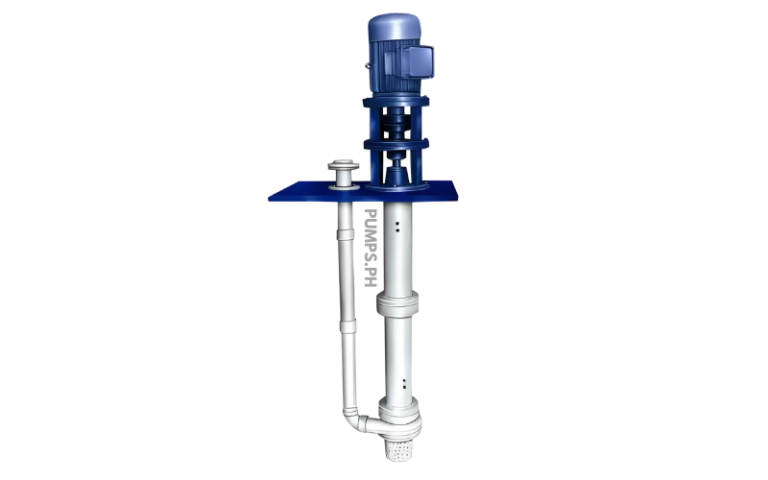
Single-Stage Vertical Sump Pump
The bearings use ball bearings with diagonal angular contact that are arranged back-to-back. The purpose of installing the bearing sleeves on the shaft is to make it easier to modify the rotor's axial position. Grease, thin oil, or lubricant tailored to specific operating conditions can be used to lubricate the bearing components. Three types of oil mist lubrication are available, and in order to satisfy the needs for on-site monitoring of bearing operation conditions, the bearing components can be fitted with vibration and temperature measurement holes.
- Clean or polluted, low temperature or high temperature
- Chemically neutral or corrosive liquids
- Refinery
- Petrochemical
- Chemical industry
- Coal chemical industry
- Power station
- Photovoltaic power generation
- Sewage treatment
- Papermaking and general industrial applications.